Caso de Éxito: Savvy Data Systems
Con el lema Boosting your digitalization (Impulsando tu digitalización en inglés), Savvy Data Systems es un proveedor de soluciones de Big Data especializado en ayudar a los fabricantes de maquinaria y herramienta industrial a mejorar la eficiencia de sus procesos productivos, facilitando su transición a la Industria 4.0. y la servitización de sus negocios. Para hacerlo, Savvy ha desplegado una plataforma Cloud Híbrida de alto rendimiento, en la que los Servidores Cloud de Arsys refuerzan la capacidad de su propia infraestructura para alcanzar una capacidad conjunta media de 700.000 transacciones de datos por segundo, que se pueden escalar de forma muy eficiente y en tiempo real en bloques de 200.000 transacciones por segundo gracias a la flexibilidad de la Nube.
Savvy nació en el seno del desarrollador de software Syslan Ingeniería para especializarse en la adquisición, tratamiento y análisis de grandes volúmenes de datos industriales. Desde 2015, cuenta entre sus accionistas mayoritarios a DANOBAT GROUP, líder europeo en fabricación de Máquina-Herramienta para nichos de alta especialización con 15 centros productivos y que emplea a más de 1.300 profesionales.
Tres años más tarde, la Plataforma 360º de Savvy ha resultado galardonada con el Premio a la Innovación en Integración de Conceptos 4.0 en Sistemas de Fabricación Avanzados concedido en la Bienal de Máquina-Herramienta de Bilbao la tercera feria industrial más importante en Europa y primera de su sector en España. En este mismo año, además, Savvy se ha incorporado al centro tecnológico vasco Digital Grinding Innovation Hub, que fomenta la investigación y el desarrollo de soluciones innovadoras en digitalización y rectificado industrial, que cuenta con esa misma plataforma de Savvy como elemento estratégico.
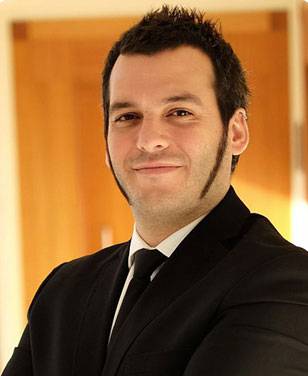
Fernando Sáenz, Director Gerente de Savvy Data Systems
En esta entrevista, Fernando Sáenz, Director Gerente de Savvy Data Systems, nos explica cómo ha evolucionado la gestión del dato en el sector industrial durante los últimos años gracias a la digitalización de sus procesos y la relación entre Cloud Computing, Big Data e Industria 4.0.
- Desde Savvy, ¿cómo entendéis la gestión y analítica del dato en los procesos de Transformación Digital de los fabricantes industriales? Los fabricantes de máquina-herramienta compiten en un sector altamente tecnológico, donde es habitual la adopción de electrónica y componentes de última generación. Dedican un importante esfuerzo para la investigación y ensayo, como medio para generar productos y generar así un conocimiento único que les aporte una ventaja competitiva. Tradicionalmente, se han centrado en las mejoras mecánicas y de automatización y están muy enfocados en la observación del mundo físico. Este enfoque, sin embargo, ha venido cambiando en los últimos años y, progresivamente, ha ido ganando fuerza la adopción de tecnologías para el análisis de grandes volúmenes de datos como medio para generar un conocimiento no obvio, que difícilmente podría ser descubierto mediante la observación física. Estas técnicas también permiten impulsar de forma notable la servitización de su negocio, ya que, entre otras capacidades, permiten detectar oportunidades de venta, servicios de mantenimiento predictivos, optimización de producción y/o proceso, etc. En Savvy, nuestro planteamiento se basa en permitir a nuestros clientes centrarse en los campos que dominan, y proveer nosotros todas las herramientas que van a necesitar para acometer sus planes de digitalización y servitización. Es decir, la entrega como servicio de tecnologías de captación, tratamiento y análisis digital de datos permite a nuestros clientes centrarse en su área de conocimiento, apalancándose sobre estas herramientas. Nuestro objetivo es transformar las tecnologías complejas de tratamiento de información en herramientas comprensibles para su uso en el sector industrial.
- ¿Cuál es la relación entre Big Data, Cloud e Industria 4.0?, ¿qué aporta el Cloud Computing a la gestión del dato? Los procesos productivos industriales se llevan a cabo habitualmente utilizando máquinas con capacidad de funcionar de manera automática o semiautomática. Esta automatización de la operación se logra mediante la inclusión de diferentes dispositivos electrónicos, como sensores, actuadores, autómatas de control, controles numéricos, etc. Simplificando al máximo, podríamos decir que una máquina está controlada por un autómata que “lee” desde los sensores la situación del proceso y, siguiendo un conjunto de reglas, toma una serie de decisiones que se materializan mediante la activación de diferentes actuadores. Pensemos, por ejemplo, en un escenario sencillo, como puede ser una cinta transportadora similar a la de un cajero de un supermercado, que debe detenerse cuando los artículos llegan al final de la cinta y queda a la espera de que alguien los recoja. El autómata activa el motor que gobierna el movimiento de la cinta, hasta que “lee” una señal de corte en la fotocélula situada al final de dicha cinta, lo que indica la presencia de un artículo en esa posición. Las máquinas industriales funcionan de manera similar, si bien son por lo general mucho más complejas e integran cientos de sensores y actuadores, diferentes circuitos de potencia, hidráulicos, neumáticos, varios autómatas de control y numerosos conjuntos de reglas organizadas en programas de control. Esta complejidad provoca que los ingenieros que trabajan en su diseño, puesta en marcha y/o mantenimiento no siempre puedan gestionar la totalidad de las situaciones que pueden darse durante la operación de la máquina. Por eso, decidimos aumentar el ciclo de vida del dato, haciendo que éste no “muera” al ser gestionado por el autómata de control, sino que además pueda ser transmitido a un repositorio de datos, donde se convierte en la materia prima de una nueva actividad de investigación y análisis. De este modo, el dato se consolida en uno o varios sistemas específicamente diseñados para facilitar tanto la ingeniería de datos como la propia ciencia alrededor de los datos , creando el espacio adecuado para la detección de patrones, aprendizaje de modelos predictivos, creación de herramientas inteligentes de optimización, etc. Es decir, todos estos datos pueden ser ahora utilizados para entender de una forma diferente la operación y situación de la máquina, por lo que se genera ese conocimiento no obvio al que hacía referencia anteriormente. La tecnología Cloud juega un papel determinante en el desarrollo de la Industria 4.0. La mayoría de los fabricantes de máquina-herramienta cuentan con un parque de máquinas muy deslocalizado, ya que tienden a ser empresas muy exportadoras. Y con Cloud, es posible conectar todas las máquinas de sus propios procesos productivos (y de los de sus clientes) a un único repositorio, haciendo posible un nivel de análisis sin precedentes en el sector industrial.
- ¿En qué estado se encuentra la denominada Industria 4.0 en España? En los últimos años, hemos visto cómo la digitalización de la industria ha empezado a tomar fuerza, si bien todavía queda un largo camino por recorrer. Las tecnologías habilitadoras básicas ya están muy maduras y se encuentran ya muy trabajadas en otros sectores, por lo que se han incorporado en general de una forma bastante satisfactoria. Hablamos aquí de tecnologías como la conectividad segura, monitorización remota, entrega de datos en dispositivos ubicuos o la gestión de plataformas virtualizadas en entornos Cloud. Podemos decir que en general la industria ya ha superado satisfactoriamente la primera fase relativa al reto que suponía incorporar estas tecnologías a sus máquinas y procesos. Ahora estamos de lleno inmersos en el siguiente estadio, que supone un reto mucho mayor, y que está estrechamente relacionado con el modelo de negocio del fabricante de máquinas y en el de sus clientes. La digitalización de los activos debe integrarse de forma adecuada en la digitalización interna que hace años ha ido implantándose en las empresas, y que ha venido materializándose en sistemas ERP, MES, GMAO, CRM, etc. Es decir, los datos generados desde las máquinas deben incorporarse de forma inteligente a los sistemas digitales que las empresas ya vienen utilizando para su operación y producción. Esta integración genera un espacio de oportunidad enorme para todos los actores que forman parte de la cadena: fabricantes de máquinas, fábricas, empresas que desarrollan software de gestión de planta, proveedores de ERP, etc.
- ¿Cuáles son los principales retos de las empresas productivas a la hora de dar el salto en esta Transformación Digital que supone la Industria 4.0? En los últimos años ha existido una barrera relacionada con la creación de las tecnologías habilitadoras necesarias para convertir la industria 4.0 en una realidad, si bien hoy en día podemos decir que las tecnologías existen, están ahí, y ahora tenemos que saber cómo utilizarlas de forma inteligente. Ahora bien, es cierto que hoy en día existen limitaciones para desplegar estas tecnologías. Una importante barrera está relacionada con la ciberseguridad y la capacidad de generar confianza hacia el cliente. Los equipos que gestionan redes operacionales (OT) son conscientes de que su grado de seguridad es muy diferente respecto al que cuentan las redes IT. Una red OT está diseñada para gestionar comunicaciones de datos en la planta y considera que éste se trata de un entorno seguro y confiable. Al unir los mundos IT y OT, surge una avalancha de amenazas para las redes operacionales que hay que saber detectar y gestionar. Por eso, la implantación de tecnologías 4.0 en una planta muchas veces depende de la confianza que seamos capaces de proyectar sobre el departamento y las redes IT. Otro reto, quizá el mayor de todos, es el de cumplir las expectativas. La industria 4.0 está mostrando un conjunto de capacidades que aviva la creatividad de los que trabajamos en ámbitos de innovación. Esto provoca que propongamos escenarios futuros muy prometedores y, con ello, nos hemos creado nosotros mismos un reto enorme en cuanto a la capacidad de crear negocio y conocimiento a partir de datos industriales. Parte de este reto está relacionado con explotar adecuadamente un conjunto de técnicas matemáticas conocidas como aprendizaje automático (el denominado machine learning), situando dichas técnicas como herramientas habilitadoras estratégicas que permitan la predicción y optimización en todo tipo de escenarios complejos.
- ¿Por qué decidisteis recurrir a las soluciones Cloud de Arsys para alojar vuestras soluciones de Big Data? Hemos estado trabajando con Arsys varios años como «consumidores». Es decir, alojando en Arsys ciertas herramientas digitales que utilizamos para nuestro día a día, pero decidimos dar un paso más y hemos desplegado en los Centros de Datos de Arsys nuestra plataforma Industrial Cloud. Fueron muchos los motivos que nos llevaron a tomar esta decisión, como el buen nivel de servicio, su velocidad y profesionalidad de respuesta, el diseño de su Centro de Datos o la agilidad, facilidad y estabilidad en todas las tareas de despliegue y mantenimiento. En nuestro caso, también resultó un elemento determinante el hecho de poder trabajar con infraestructuras situadas físicamente en España. Con el tiempo, nuestra elección no ha hecho más que confirmarse con el nivel de servicio que Arsys nos ofrece, del que podemos destacar la facilidad de gestión, la flexibilidad total para el despliegue de arquitecturas complejas o el hecho de poder gestionar de forma automática los recursos, ajustándolos a la demanda real, ya que la plataforma puede autodimensionar sus diferentes capas.
- ¿Qué solución os propuso Arsys para vuestro negocio? A lo largo de los últimos años, hemos venido haciendo un despliegue progresivo, llevado a cabo por nuestro equipo de infraestructuras. Trabajar para entornos industriales requiere crear soluciones IT de alto rendimiento, dado el gran volumen de datos heterogéneos que son capaces de transmitir las máquinas de nuestros clientes. Para poder tratar toda esta información, nuestra plataforma Industrial Cloud está soportada por una arquitectura compleja, que nos ha llevado a acometer el despliegue en distintas fases. En cada fase desplegamos diferentes capas de operación, y realizamos varias pruebas de rendimiento y estabilidad, sometiendo a la arquitectura a diversos test de estrés. Nuestra plataforma es híbrida. El núcleo de control de operación de la plataforma está completamente desplegado en un Centro de Datos de Arsys, donde contamos con seis paneles para gestionar nuestros Servidores Cloud. También disponemos de servidores en nuestras propias instalaciones en San Sebastián y Elgoibar y capacidad de cómputo distribuida instalada en cada máquina. Esta infraestructura está formada por 22 servidores en capa principal de operación, 15 servidores en el nivel de BI & ML y 10 servidores en la capa de servicio a plataforma, todos ellos de alto rendimiento. Nuestro alcance actual de cómputo, incluyendo la capacidad distribuida, es de 1.300 núcleos y 1,5 TB de RAM. Tenemos capacidad para procesar unas de 700.000 transacciones de datos por segundo (42 millones por minuto), que podemos escalar horizontalmente en tiempo real y con coste muy reducido, que podemos aumentar instantáneamente en bloques de 200.000 transacciones por segundo.
- ¿Qué ventajas aporta a vuestros clientes que contéis con una infraestructura en Cloud? Hay que tener en cuenta que la servitización en la industria es todavía un mercado que está despertando. Nuestro equipo lleva 8 años trabajando con clientes que están inmersos en este proceso, y algunos de ellos ya han empezado a vender productos y servicios digitales que complementan sus productos industriales. Para estos clientes, la plataforma aporta un nuevo modelo de negocio, nuevas capacidades para su equipo y, en definitiva, nuevos productos y servicios que complementan su cartera, que suponen ingresos directos y posicionan su marca como un referente tecnológico en su sector. Ahora bien, llegar a ese punto de madurez no es sencillo. No estamos hablando de una plataforma de monitorización, sino de crear y desplegar productos y servicios basados en la predicción y en la optimización, que impactan de forma significativa en la cuenta de resultados del cliente final. La creación de estos productos y servicios supone no solo la integración de tecnología, el equipo de Savvy, además, tiene que comprender cómo funcionan las máquinas de nuestros clientes, cuál es su propuesta de valor y así identificar cuáles serán las implantaciones y desarrollos tecnológicos que crearán las mejores oportunidades para conformar los nuevos productos y servicios. Es un camino complejo, cuya duración y resultado depende mucho de nuestro cliente, con el que trabajamos en un esquema de colaboración muy estrecha, y al que acompañamos en todo este camino tan complejo. Es por eso que el lema de Savvy es Boosting your digitalization. Nuestro objetivo es acelerar drásticamente la digitalización de los productos y servicios de nuestros clientes, reduciendo significativamente el riesgo que supone la apuesta por este camino.
- ¿Cuál es el papel del actual proveedor Cloud en el desarrollo de la Industria 4.0 y de las soluciones que empresas como Savvy desarrollan para un tercero? El trabajo de digitalización en la industria es complejo y puede llegar a ser muy costoso, ya que requiere la incorporación de muchísimo equipamiento. El proveedor Cloud permite que los proyectos de digitalización del sector industrial puedan ser más flexibles, al permitir incorporar infraestructura en un modelo de pago por uso. Además, dicha infraestructura puede ir creciendo de forma dinámica, a medida que lo hagan las necesidades del proyecto. De esta forma, Cloud reduce una parte importante del riesgo, al no tener que realizar grandes inversiones iniciales en equipamiento, y aportar un entorno flexible que acompaña y favorece el crecimiento del proyecto. Otro factor interesante es la reducción en el coste de mantenimiento físico del equipamiento, que es inherente al contrato de pago por uso y que, además, permite situar a los proyectos en altos niveles de servicio (SLA) con un coste contenido.
- Con esta experiencia, ¿tenéis previsto seguir trabajando sobre infraestructura Cloud para desarrollas vuestras soluciones? La plataforma de Savvy está en continuo crecimiento, conectamos aproximadamente unas 150 máquinas nuevas cada semestre, lo que supone un aumento constante en la capacidad de cómputo y almacenamiento necesaria. Además, el acompañamiento que hacemos con nuestros clientes permite que surjan nuevas ideas que, muchas de ellas, terminan siendo materializadas en forma de más y mejor inteligencia Cloud, lo cual también implica necesidad de crecimiento en infraestructura. Podríamos decir que la flexibilidad y capacidad de autogestión que nos aporta Arsys forma ya parte de nuestra forma de trabajar del día a día. Contamos con ello para nuestros proyectos internos de investigación, para los proyectos de innovación que lanzamos con nuestros clientes, para la creación y despliegue de los productos y servicios finales que comercializan nuestros clientes, e incluso para los programas para digitalización de la industria que Europa ha lanzado como estratégicos, en los que trabajamos actualmente (ECSEL, H2020, FOF-09). Actualmente, la infraestructura Cloud de Arsys está siendo utilizada, a través de nuestra plataforma, por todo tipo de actores clave en la digitalización de la industria europea, desde fabricantes de máquina-herramienta hasta prestigiosas universidades, en países como España, Alemania, Italia, Francia, Suecia, Noruega, Finlandia, Holanda, Hungría, Grecia, Irlanda, o Austria.